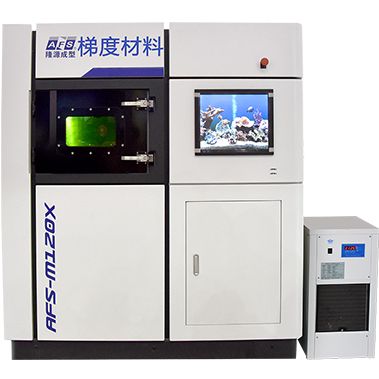
SLM 3D принтеры. Печать металлами
ГРАДИЕНТНый 3D принтер SLM
How we work
m120x(Т) - Печать одновременно несколькими металлами
Уникальная система 3Д печати несколькими металлами одновременно! Изготовление градиентных сплавов с индивидуальными пропорциональными характеристиками может быть достигнуто путем настройки механизма подачи порошка.Позволяет получать двухфазные/многофазные градиентные материалы с полным пропорциональным изменением в одном изделии.
AFS-M120X демонстрирует стабильную и высокопроизводительную подготовку материалов, позволяет осуществлять характеристику градиентных сплавов, таких как SS316L-CoCrMo, Inconel 718-CoCrMo и Ti-Ta (открытие новых материалов), и показала высокий потенциал коммерческого применения.
Применение
Подходит для исследований и разработок в области производства изделий из композитных металлических материалов
Материалы
Система подачи порошка может обеспечивать равномерный градиент и точную подачу порошка из двух или более металлических материалов
Нержавеющая сталь, титановый сплав, алюминиевый сплав, штамповая сталь, сплав кобальта и хрома, сплав на основе никеля и т. д.
Область построения
120х150x150 - модель AFS-M120XT
120x120x150 - модель AFS-M120X
Патент AFS
Устройство и способ получения градиентных материалов на основе технологии Селективного Лазерного Сплавления (SLM) ZL201810292599.9 PCT/CN2019/076890
Технические характеристики
|
| ||
---|---|---|---|
|
Модель | AFS-M120X | AFS-M120XT |
|
Градиентная функция | Горизонтальный градиент | Горизонтальный градиент +вертикальный градиент |
|
Тип лазера | Волоконный лазер IPG 500 Вт | Волоконный лазер IPG 500 Вт |
|
Область печати | 120×120×150 мм | 120×150×150 мм |
Максимальная скорость сканирования | 6 м/с | 6 м/с | |
Скорость печати | 2-20см3/ч | 2-20см3/ч | |
Материалы | Нержавеющая сталь, титановый сплав, алюминиевый сплав, штамповая сталь, сплав кобальта и хрома, сплав на основе никеля и т.д. | Нержавеющая сталь, титановый сплав, алюминиевый сплав, штамповая сталь, сплав кобальта и хрома, сплав на основе никеля и т.д. | |
Толщина слоя | 0,02~0,1 мм | 0,02~0,1 мм | |
Размер частиц порошка | 15-53 мкм | 15-53 мкм | |
Точность позиционирования лазерного луча (ость XY) | ±5 мкм | ±5 мкм | |
Точность построения | ±0,1 мм/100 мм | ±0,1 мм/100 мм | |
Требования к питанию | 380 В переменного тока/50 Гц/8 кВт | 380 В переменного тока/50 Гц/8 кВт | |
Габариты | 1532×1390×1830 мм | 1532×1390×1830 мм |
ПРИМЕРЫ ПРИМЕНЕНИЯ
SLM 3D принтер AFS-M120
How we work
m120 - 3D печать металлом
Используется классическая технология 3Д печати SLM.
Применение
Мелкосерийное производство геометрически сложных изделий
Материалы
Нержавеющая сталь, титановый сплав, алюминиевый сплав, штамповая сталь, сплав кобальта и хрома, сплав на основе никеля и т. д.
Область построения
120x120x150 - модель AFS-M120
Лазер
Волоконный лазер IPG 500 Вт
Технические характеристики
|
|
|
---|---|---|
|
Модель | AFS-M120 |
|
Тип лазера | Волоконный лазер IPG 500 Вт |
|
Область печати | 120×120×150 мм |
Максимальная скорость сканирования | 6 м/с | |
Скорость печати | 2-20см3/ч | |
Материалы | Нержавеющая сталь, титановый сплав, алюминиевый сплав, штамповая сталь, сплав кобальта и хрома, сплав на основе никеля и т.д. | |
Толщина слоя | 0,02~0,1 мм | |
Размер частиц порошка | 15-53 мкм | |
Точность позиционирования лазерного луча (ость XY) | ±5 мкм | |
Точность построения | ±0,1 мм/100 мм | |
Требования к питанию | 380 В переменного тока/50 Гц/8 кВт | |
Габариты | 1532×1390×1830 мм |
Примеры применения
SLM 3D ПРИНТЕР AFS-M260
How we work
m260 - 3D ПЕЧАТЬ МЕТАЛЛОМ
Используется классическая технология 3Д печати SLM с увеличенной областью построения.
Применение
Мелкосерийное производство геометрически сложных изделий
Материалы
Нержавеющая сталь, титановый сплав, алюминиевый сплав, штамповая сталь, сплав кобальта и хрома, сплав на основе никеля и т.д.
Область построения
260х260x320 - модель AFS-M260
ЛАЗЕР
Волоконный лазер IPG 500 Вт
Технические характеристики
|
|
|
---|---|---|
|
Модель | AFS-M120X |
|
Тип лазера | Волоконный лазер IPG 500 Вт |
|
Область печати | 260×260×320 мм |
Максимальная скорость сканирования | 6 м/с | |
Скорость печати | 2-20см3/ч | |
Материалы | Нержавеющая сталь, титановый сплав, алюминиевый сплав, штамповая сталь, сплав кобальта и хрома, сплав на основе никеля и т.д. | |
Толщина слоя | 0,02~0,1 мм | |
Размер частиц порошка | 15-53 мкм | |
Точность позиционирования лазерного луча (ость XY) | ±5 мкм | |
Точность построения | ±0,1 мм/100 мм | |
Требования к питанию | 380 В переменного тока/50 Гц/8 кВт | |
Габариты | 2925×1056×2135 мм |
Примеры применения
SLM - технология 3д печати
Селективное лазерное плавление (SLM)
Селективное лазерное плавление ( SLM ) — это одно из многих частных названий технологии аддитивного производства металлов, в которой для создания металлических деталей используется слой порошка с источником тепла. Также известное как прямое лазерное плавление металла ( DMLM ), стандартный термин ASTM — плавление в порошковом слое ( PBF ). PBF — это метод быстрого прототипирования, 3D-печати или аддитивного производства ( аддитивного производства), предназначенный для использования лазера с высокой плотностью мощности для плавления и сплавления металлических порошков.
История
Селективное лазерное плавление является одной из многих запатентованных технологий плавления в порошковом слое, начатых в 1995 году в Институте Фраунгофера ILT в Аахене , Германия, в рамках немецкого исследовательского проекта, в результате которого был получен так называемый базовый патент ILT SLM DE 19649865. Уже во время на его начальном этапе д-р Дитер Шварце и д-р Матиас Фокеле из F&S Stereolithographietechnik GmbH, расположенной в Падерборне , сотрудничали с исследователями ILT д-ром Вильгельмом Майнерсом и д-ром Конрадом Виссенбахом. В начале 2000-х F&S заключила коммерческое партнерство с MCP HEK GmbH (позже переименованной в MTT Technology GmbH, а затем в SLM Solutions GmbH), расположенной в Любеке на севере Германии.
Комитет по стандартизации ASTM International F42 отнес селективное лазерное плавление к категории «лазерного спекания», хотя это общепризнанное неправильное название, поскольку этот процесс полностью плавит металл в твердую однородную массу, в отличие от селективного лазерного спекания (SLS), которое является истинным процесс спекания. Другое название селективного лазерного плавления — прямое лазерное спекание металла (DMLS), название, присвоенное торговой маркой EOS, однако оно вводит в заблуждение относительно реального процесса, поскольку деталь плавится во время производства, а не спекается, что означает, что деталь полностью плотная. Этот процесс во всех отношениях очень похож на другие процессы SLM и часто рассматривается как процесс SLM.
Похожим процессом является электронно-лучевая плавка (ЭЛП), в которой в качестве источника энергии используется электронный луч.
Процесс
SLM 3D принтеры используют различные сплавы, что позволяет создавать прототипы функционального оборудования из того же материала, что и серийные компоненты. Поскольку компоненты строятся слой за слоем, можно проектировать органическую геометрию, внутренние элементы и сложные проходы, которые невозможно отлить или обработать каким-либо иным образом. SLS 3D принтер производит прочные и долговечные металлические детали, которые хорошо работают как в качестве функциональных прототипов, так и в качестве производственных деталей для конечного использования.
Процесс начинается с разделения данных файла 3D CAD на слои, обычно толщиной от 20 до 100 микрометров, с созданием 2D-изображения каждого слоя; этот формат файла является отраслевым стандартным файлом .stl , используемым в большинстве технологий многослойной 3D-печати или стереолитографии. Затем этот файл загружается в пакет программного обеспечения для подготовки файлов, который назначает параметры, значения и физическую поддержку, что позволяет интерпретировать и создавать файл с помощью различных типов машин для аддитивного производства.
При селективном лазерном плавлении тонкие слои распыленного тонкого металлического порошка равномерно распределяются с помощью механизма покрытия на подложку, обычно металлическую, которая крепится к делительному столику, который перемещается по вертикальной оси (Z). Это происходит внутри камеры, содержащей строго контролируемую атмосферу инертного газа , аргона или азота с содержанием кислорода ниже 500 частей на миллион. После распределения каждого слоя каждый двумерный срез геометрии детали сплавляется путем выборочного плавления порошка. Это достигается с помощью мощного лазерного луча, обычно иттербиевого волоконного лазера мощностью в сотни ватт. Лазерный луч направляется в направлениях X и Y с помощью двух высокочастотных сканирующих зеркал. Энергия лазера достаточно интенсивна, чтобы обеспечить полное плавление (сварку) частиц с образованием твердого металла. Процесс повторяется слой за слоем, пока деталь не будет готова.
В 3D принтере SLM используется мощный Yb-оптический лазер мощностью 200 Вт и более. Внутри рабочей камеры есть платформа для дозирования материала и платформа для сборки, а также лезвие для повторного нанесения покрытия, используемое для перемещения нового порошка по платформе для сборки. Технология сплавляет металлический порошок в твердую деталь, расплавляя его локально с помощью сфокусированного лазерного луча. Детали создаются аддитивно (послойно) слой за слоем, обычно с использованием слоев толщиной 20 микрометров.
Материалы
3D принтеры для селективной лазерной плавки (SLM) могут работать с рабочим пространством до 1 м (39,37 дюйма) по осям X, Y и Z. Некоторые из материалов, используемых в этом процессе, могут включать суперсплавы на основе никеля, медь, алюминий, нержавеющая сталь, инструментальная сталь, кобальт-хром, титан и вольфрам. SLM 3D принтер особенно полезен для изготовления деталей из вольфрама из-за высокой температуры плавления и высокой температуры вязко-хрупкого перехода этого металла. Чтобы материал можно было использовать в процессе, он должен находиться в распыленной форме (в форме порошка).
Эти порошки обычно представляют собой предварительные сплавы, распыляемые газом, что является наиболее экономичным процессом получения сферических порошков в промышленных масштабах. Желательна сферичность, поскольку она гарантирует высокую текучесть и плотность упаковки, что приводит к быстрому и воспроизводимому распределению слоев порошка. Для дальнейшей оптимизации текучести обычно используются узкие гранулометрические составы с низким процентным содержанием мелких частиц, таких как 15–45 мкм или 20–63 мкм. Доступные в настоящее время сплавы, используемые в процессе, включают нержавеющую сталь 17-4 и 15-5 , мартенситностареющую сталь , кобальт - хром , инконель 625 и 718. алюминий [14] AlSi10Mg и титан Ti6Al4V.
Механические свойства образцов, изготовленных методом прямого лазерного спекания металлов, отличаются от образцов, изготовленных методом литья. Образцы AlSiMg, изготовленные с использованием прямого лазерного спекания металла, демонстрируют более высокий предел текучести , чем образцы, изготовленные из коммерческого литого сплава A360.0 , на 43 % в плоскости xy и на 36 % в плоскости z. Хотя было показано, что предел текучести AlSiMg увеличивается как в плоскости xy, так и в плоскости z, удлинение при разрыве уменьшается в направлении наращивания. Такое улучшение механических свойств образцов, полученных методом прямого лазерного спекания металлов, объясняется очень тонкой микроструктурой.
Добавка следующего поколения производится посредством процесса прямого лазерного плавления металла (SLM). Слои были разработаны таким образом, чтобы обеспечить расплавление порошка непосредственно перед формированием поверхности. Кроме того, давление промышленности добавило больше порошков суперсплава к доступной обработке, включая AM108. Не только операция печати и ориентация обеспечивают изменение свойств материала, но и необходимая постобработка с помощью термообработки горячим изостатическим давлением (HIP) и дробеструйной обработки, которые изменяют механические свойства до уровня заметной разницы по сравнению с равноосным литые или кованые материалы.
На основе исследований, проведенных в Токийском столичном университете, показано, что предел ползучести и пластичность обычно ниже для суперсплавов на основе никеля с аддитивной печатью по сравнению с деформируемым или литым материалом. Направленность печати является основным влияющим фактором наряду с размером зерна. Кроме того, как показали исследования, проведенные с добавкой Inconel 718, износостойкость обычно лучше из-за состояния поверхности; исследование также продемонстрировало влияние мощности лазера на плотность и микроструктуру.
Плотность материала, создаваемая во время параметров лазерной обработки, может дополнительно влиять на поведение трещины, так что повторное раскрытие трещины после процесса HIP уменьшается при увеличении плотности. Крайне важно иметь полное представление о материале, а также о его обработке от печати до требуемой постпечатной обработки, чтобы иметь возможность окончательно определить механические свойства для использования в дизайне.
Обзор и преимущества
Селективное лазерное плавление (SLM) — это часть аддитивного производства, при которой лазер с высокой плотностью мощности используется для плавления и сплавления металлических порошков. Это быстро развивающийся процесс, который реализуется как в исследованиях, так и в промышленности. Селективное лазерное плавление также известно как прямое лазерное плавление или плавление в лазерном слое. Это достижение очень важно как для науки о материалах, так и для промышленности, потому что оно может не только создавать пользовательские свойства, но и сокращать использование материалов и давать больше степеней свободы при проектировании, чего невозможно достичь с помощью производственных технологий. Селективное лазерное плавление очень полезно как штатному инженеру по материалам, так и инженеру-технологу. Такие запросы, как требование быстрого производства материала или наличие конкретных приложений, требующих сложной геометрии, являются распространенными проблемами, возникающими в промышленности. Наличие SLM 3D принтера действительно улучшит процесс не только создания, но и позволит создавать 3Д печатные изделия со сложной геометрией недоступной для традиционного производства. Текущие проблемы, связанные с SLM, связаны с ограничением обрабатываемых материалов, неразработанными настройками процесса и металлургическими дефектами, такими как растрескивание и пористость.[20] Проблемы будущего заключаются в невозможности создания полностью плотных деталей из алюминиевых сплавов. Алюминиевые порошки легкие, обладают высокой отражательной способностью, высокой теплопроводностью и низким лазерным поглощением в диапазоне длин волн волоконных лазеров, которые используются в SLM 3D принтерах.
Эти проблемы можно решить, проведя дополнительные исследования того, как материалы взаимодействуют при сплавлении друг с другом.
Механические свойства
Механические свойства сплавов, синтезированных методом SLM 3Д печати, могут существенно отличаться от свойств их аналогов, изготовленных традиционным способом. Сообщалось об увеличении прочности на растяжение и ударной вязкости никелевых сплавов, алюминиевых сплавов и Ti - 6Al - 4V . Однако усталостная прочность сплавов, изготовленных методом SLM, значительно уступает прочности литых сплавов. Отклонения в механических свойствах объясняются уникальной микроструктурой дефектов, созданные в процессе SLM, а также структурные возможности и ограничения материалов, произведенных с помощью аддитивного производства, являются активной областью исследований в области материаловедения.
Основной характеристикой сплавов, изготовленных методом SLM, является большая анизотропия механических свойств. В то время как структура зерен в литых металлах обычно характеризуется примерно однородными изотропными зернами, сплавы, изготовленные методом SLM, демонстрируют значительное удлинение зерен в направлении сборки. Анизотропия зернистой структуры связана с анизотропией распределения дефектов, направления распространения трещины и, в конечном счете, механических свойств со значительным снижением жесткости , прочности и пластичности при растягивающем напряжении, ориентированном параллельно, по сравнению с перпендикулярным. , в направлении сборки.
Применение
Типы применений, наиболее подходящие для процесса селективной лазерной плавки, — это изделия сложной геометрии и структуры с тонкими стенками и скрытыми пустотами или каналами, с одной стороны, или небольшими партиями, с другой стороны. Преимущество может быть получено при производстве гибридных форм, когда твердая и частично сформированная или решетчатая геометрия могут быть получены вместе для создания единого объекта, такого как ножка бедра или вертлужная чашка или другой ортопедический имплантат, где остеоинтеграция усиливается за счет геометрии поверхности. Большая часть новаторских работ с технологиями селективного лазерного плавления приходится на легкие детали для аэрокосмической промышленности, где традиционные производственные ограничения, такие как инструменты и физический доступ к поверхностям для обработки, ограничивают конструкцию компонентов. SLM 3D принтер позволяет создавать детали послойно (аддитивно), чтобы формировать компоненты почти чистой формы, а не путем удаления лишнего материала.
Традиционные производственные технологии имеют относительно высокую стоимость установки (например, для создания пресс-формы). Хотя SLM 3Д печать имеет высокую стоимость в расчете на одну деталь (в основном из-за того, что требует много времени), рекомендуется производить только очень небольшое количество деталей. Это относится, например, к запасным частям старых машин (таких как старинные автомобили) или к отдельным продуктам, таким как имплантаты.
Испытания, проведенные Центром космических полетов им. Маршалла НАСА , который экспериментирует с технологией изготовления некоторых трудноизготавливаемых деталей из никелевых сплавов для ракетных двигателей J-2X и RS-25 , показывают, что трудноизготавливаемые детали, изготовленные с помощью этой технологии, несколько слабее, чем кованые и фрезерованные детали, но часто избегают сварки, которая является слабым местом.
Эта технология используется для изготовления прямых деталей для различных отраслей промышленности, включая аэрокосмическую, стоматологическую, медицинскую и другие отрасли промышленности, в которых используются детали малого и среднего размера, очень сложные детали, а также инструментальная промышленность для изготовления вставок для прямой оснастки. DMLS — это очень эффективная с точки зрения затрат и времени технология. Эта технология используется как для быстрого прототипирования, так как сокращает время разработки новых продуктов, так и для серийного производства как метод экономии средств для упрощения сборок и сложной геометрии. [32] С типичными размерами сборки 250 x 250 x 325 мм и возможностью «выращивания» нескольких деталей одновременно.
Северо-Западный политехнический университет Китая использует аналогичную систему для изготовления конструкционных титановых деталей для самолетов. Исследование EADS показывает, что использование этого процесса позволит сократить количество материалов и отходов в аэрокосмических приложениях.
5 сентября 2013 года Илон Маск опубликовал в Твиттере изображение камеры ракетного двигателя SpaceX SuperDraco с регенеративным охлаждением , выходящей из металлического 3D-принтера SLM, отметив, что она состоит из суперсплава Inconel. Неожиданно SpaceX объявила в мае 2014 года, что летная версия двигателя SuperDraco полностью напечатана и является первым полностью напечатанным ракетным двигателем. Используя Inconel, сплав никеля и железа, аддитивно изготовленный путем прямого лазерного спекания металла, двигатель работает при давлении в камере 6900 килопаскалей (1000 фунтов на квадратный дюйм) при очень высокой температуре. Двигатели заключены в защитную гондолу с печатью, также напечатанную SLM, чтобы предотвратить распространение неисправности в случае отказа двигателя. Двигатель прошел полные квалификационные испытания в мае 2014 года, и его первый орбитальный космический полет запланирован на апрель 2018 года.
Возможность 3D-печати сложных деталей была ключом к достижению цели снижения массы двигателя. По словам Илона Маска , «это очень сложный двигатель, и было очень трудно сформировать все каналы охлаждения, головку инжектора и дроссельный механизм. создать движок SuperDraco таким, какой он есть». Процесс 3D-печати для двигателя SuperDraco значительно сокращает время выполнения заказа по сравнению с традиционными литыми деталями и «обладает превосходной прочностью, пластичностью и сопротивлением разрушению с меньшей изменчивостью свойств материалов ».
Также в 2018 году FDA одобрило первый в мире имплантат позвоночника, напечатанный на 3D-принтере из титана с использованием SLM 3D принтера.
Применение в промышленности
Аэрокосмическая отрасль — воздуховоды, приспособления или крепления для специальных авиационных приборов, лазерное спекание отвечает потребностям как коммерческой, так и военной аэрокосмической отрасли.
Производство. Лазерное спекание может обслуживать нишевые рынки с небольшими объемами по конкурентоспособным ценам. Лазерное спекание не зависит от эффекта масштаба, что освобождает от необходимости фокусироваться на оптимизации размера партии.
Медицина. Медицинские устройства представляют собой сложные и дорогостоящие изделия. Они должны точно соответствовать требованиям клиентов. Эти требования вытекают не только из личных предпочтений оператора: также необходимо соблюдать правовые требования или нормы, которые сильно различаются в зависимости от региона. Это приводит к множеству разновидностей и, следовательно, к небольшим объемам предлагаемых вариантов.
Прототипирование. Лазерное спекание может помочь, делая доступными дизайнерские и функциональные прототипы. В результате функциональное тестирование может быть начато быстро и гибко. В то же время эти прототипы можно использовать для оценки потенциального принятия продукта клиентами.
Инструментальная обработка — прямой процесс исключает создание траектории движения инструмента и несколько процессов обработки, таких как электроэрозионная обработка. Инструментальные вставки изготавливаются за ночь или даже всего за несколько часов. Также свобода проектирования может быть использована для оптимизации производительности инструмента, например, путем интеграции в инструмент конформных охлаждающих каналов.
Другие применения
Детали с полостями, подрезами, углами уклона
Подгонка, форма и функциональные модели
Инструменты, приспособления и приспособления
Конформные охлаждающие каналы
Роторы и рабочие колеса
Сложный брекетинг
SLM 3D принтеры позволяют изготавливать изделия со сложной геометрией и высокой точностью. SLM 3D принтеры нашли свое применение в аэрокосмической отрасли, ВПК, автомобильной промышленности, имплантологии и медицине.
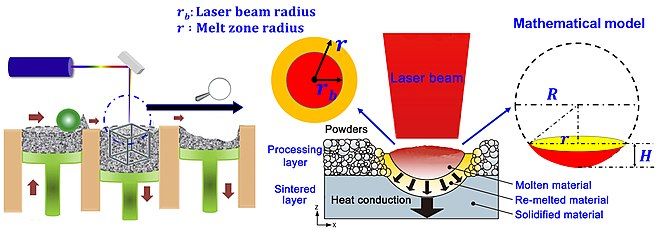
Схема селективного лазерного плавления и теплообмена в ванне расплава
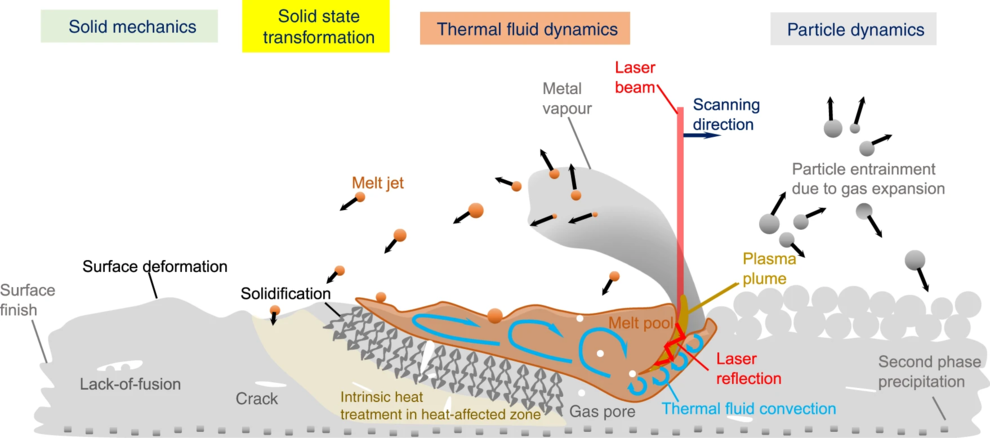
Схема основных дефектов и микроструктурных явлений, созданных с помощью 3D-печати, в отношении SLM, особенно в отношении твердотельных преобразований, динамики теплового флюида и динамики частиц
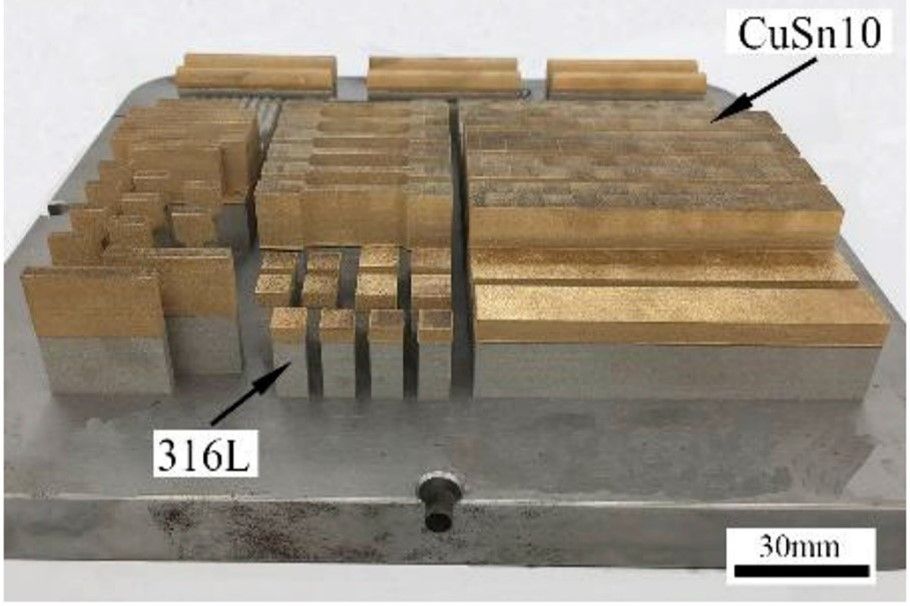
Градиентная SLM 3d печать из нескольких материалов в одном изделии. Образец распечатан на SLM 3Д принтере AFS-M120X
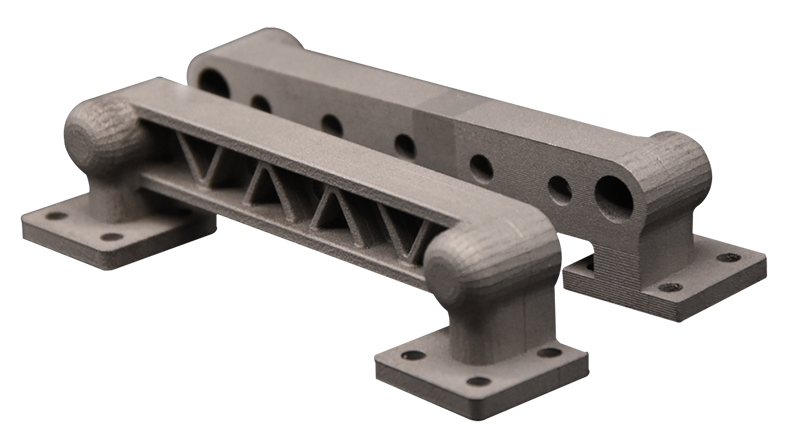
Инструментальная и нержавеющая сталь 316L (печать двумя материалами одновременно). Образец печати на градиентом SLM 3Д принтере AFS-M120X.
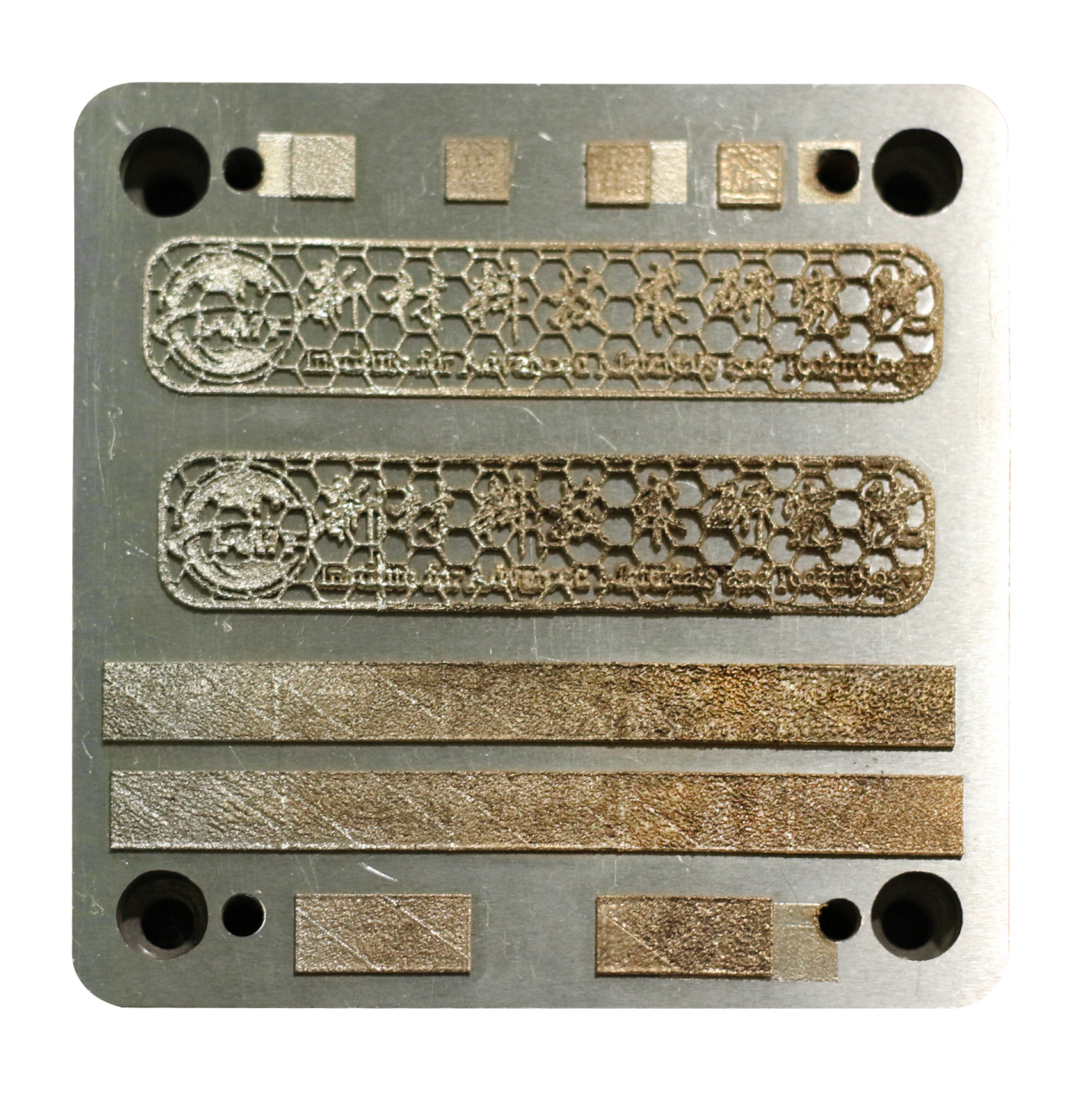
Градиентная 3Д печать - композит из нержавеющей стали 316L + Медный сплав с непрерывным градиентом.
Образец печати на градиентом SLM 3Д принтере AFS-M120X.
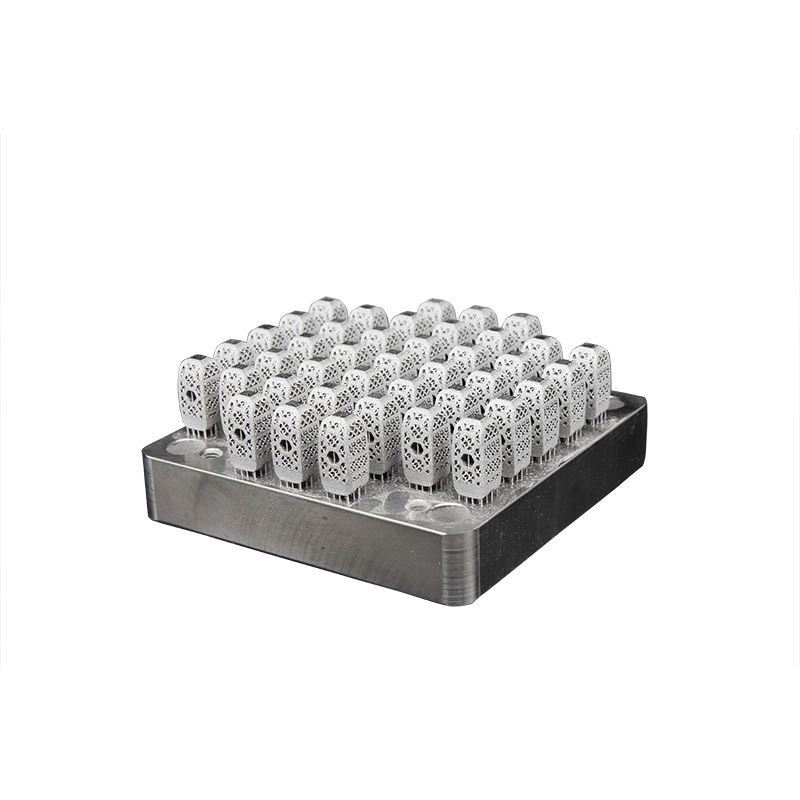
Образец печати на SLM 3D принтере AFS-120