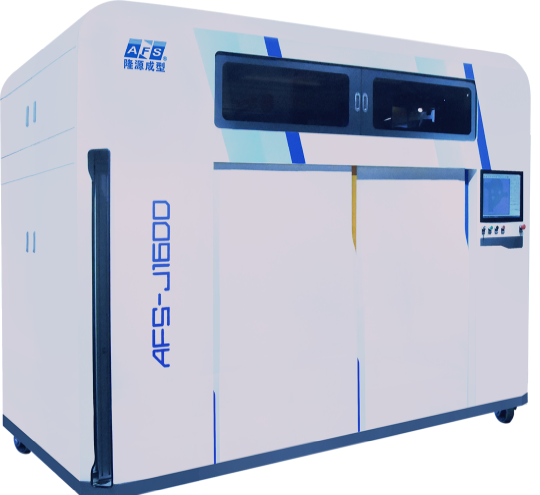
Binderjet 3D принтеры. Изготовление песочных форм.
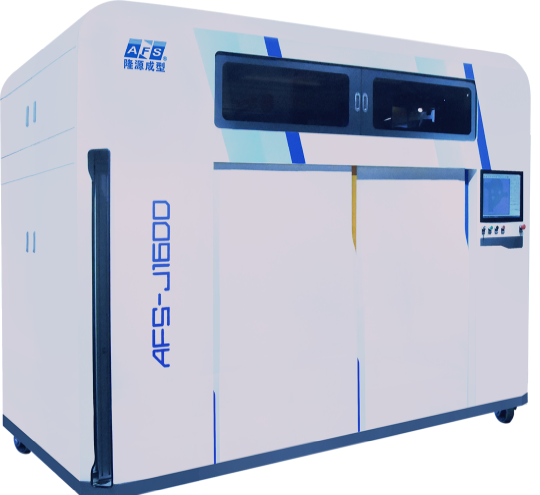
AFS-J1600. 3D Принтер Binderjet для изготовления песчаных форм
How we work
AFS-J1600. 3D ПРИНТЕР BINDERJET ДЛЯ ИЗГОТОВЛЕНИЯ ПЕСЧАНЫХ ФОРМ
3D принтер AFS позволяет изготавливать песочные формы. 3D принтер AFS рассчитан на промышленное производство, что подтверждается эксплуатацией этих машин на многих литейных предприятиях.
Применение
Изготовление песчаных форм
Материалы
Кварцевый песок, керамический песок
Химия: фурановая смола с кислотным активатором, фенольные смолы
Область построения
1600×800×600 мм - Модель: AFS-J1600
2100×1300×700 мм - Модель: AFS-J2100
Особенности
Индустриальный 3Д принтер рассчитан для непрерывного производственного процесса
Технические характеристики
|
| ||
---|---|---|---|
|
Модель | AFS-J1600 | AFS-J2100 |
|
Область печати | 1600×800×600 мм | 2100×1300×700 мм |
Скорость печати | 20-30см3/ч | 25-35см3/ч | |
Материалы | Кварцевый песок, керамический песок | Кварцевый песок, керамический песок | |
Толщина слоя | 0,2-0,5 мм | 0,2-0,5 мм | |
Разрешение сопла | 400 точек на дюйм | 400 точек на дюйм | |
Точность построения | ±0,3 мм | ±0,3 мм | |
Требования к питанию | 380 В переменного тока/50 Гц/25 кВт | 380 В переменного тока/50 Гц/35 кВт | |
Габариты | 3380×2060×3180 мм | 5500×3000×4600 мм |
ПРИМЕРЫ ПРИМЕНЕНИЯ
SD печать форм для литья
При литье в песчаные формы создаются путем уплотнения песка вокруг рисунка в коробке для форм; затем рисунок вытаскивается и остается полость в его форме. Затем расплавленный металл заливается в полость для получения компонентов. Уменьшение пористости, улучшение микроструктуры и контроль качества размеров и дефектов являются тремя наиболее распространенными проблемами при литье, но использование правильно спроектированной формы может помочь.
- “Стоимость изготовления пресс-формы со сложной геометрией является одним из основных ограничений при ее разработке. Однако AM позволяет моделировать сложные конструкции, избегая этого ограничения”, - пояснили исследователи.
3D-печать “наиболее подходит для изготовления сердечников и вставок” для пресс-форм. Но большинство исследований было сосредоточено только на конкретных параметрах, поэтому эта команда сосредоточилась на том, насколько реально выполнить 3D-печать формы, а затем сравнила ее с формой, изготовленной с помощью традиционного литья в песок.
- “Чтобы доказать полезность этой современной технологии, были изготовлены две различные формы для литья: первая была изготовлена в виде традиционного литья из песка, а вторая была изготовлена с использованием технологии 3DP. Как только формы были изготовлены, в них заливали алюминий. Затем мы проанализировали время изготовления, скорость охлаждения, отклонение размеров, качество поверхности, пористость поверхности и возможные дефекты, сравнив оба метода”, - написали они. “С помощью этого анализа мы стремились определить, применима ли технология 3DP для литья алюминия, позволяющая повысить эффективность конструкции и снизить затраты на производство”.
Они использовали литейный сплав серии AlSi для проектирования детали, а затем разработали и рассчитали систему наполнения (литник, колодец, направляющая, ворота и стояк) для форм. Для изучения поведения потока расплава с целью оптимизации системы наполнения использовался анализ конечных элементов (FEA) для моделирования заполнения и затвердевания деталей во время литья, а также создаваемой турбулентности и распределения газа, увлекаемого в жидкость. Команда использовала программное обеспечение CATIA v5 r21 для создания 3D-модели детали и обеих пресс-форм, а затем пресс-формы были изготовлены.
- “Для изготовления формы для литья песка был изготовлен разделенный шаблон методом моделирования плавленого осаждения (FDM) с помощью машины Ultimaker 2+”, - объяснила команда. “Образец содержал деталь и систему наполнения".
Алюминиевый сплав заливали, происходил процесс плавления, и они измеряли температуру формы “с помощью термической пары типа K, локализованной на расстоянии 2 мм от полости формы”.
- “Чтобы добиться правильной заливки для литья в песок, необходимо было зафиксировать половинки форм. Для техники 3DP необходимо было установить форму на песчаное основание, чтобы предотвратить движение во время литья. Впоследствии металл заливали в различные формы”, - писали исследователи.
- “Наконец, алюминиевый сплав был затвердевшим, и отливка была извлечена из обеих форм путем вибрации и крошения. Системы наполнения были разрезаны, а детали очищены воздухом под давлением, чтобы начать этап анализа”.
Они сравнили качество размеров, шероховатость, пористость и общие дефекты, используя сначала структурный световой сканер Breuckmann Smart SCAN3D-HE для их анализа и обработки облаков точек с помощью программного обеспечения Geomagic Control X. Профилометр измерил шероховатость поверхности, а отлитые детали были разрезаны и отполированы алмазной пастой толщиной 3 мкм, затем сфотографированы камерой Leica Kl 1500 для оценки внутренней пористости. Для анализа изображений использовалось программное обеспечение ImageJ от Национального института здравоохранения (NIH).
Стандартные правила проектирования были соблюдены при создании песчаной формы, которая включает в себя разливочную чашу и конический литник, заканчивающийся колодцем. Но из-за свободы дизайна, которую дает 3D-печать, этой детали не требовалась круглая геометрия, чтобы “избежать углов наклона” и “получить правильное удаление рисунка” без повреждения формы. Кроме того, 3D - печать позволила исследователям “оптимизировать систему наполнения” в пресс-форме.
- “Два цилиндрических затвора были соединены с полостью детали”, - писали они. “Благодаря этому усовершенствованию удалось устранить скважину и уменьшить размеры системы наполнения, как показано на рисунке 2с. Общий объем формы 3DP составлял 449 см3, выход металла составлял 49,75%, а вес формы составлял 0,55 кг. По сравнению с литьем из песка выход металла был оптимизирован на 29%, а вес формы был на 95% ниже”.
Чтобы избежать турбулентности металла, оксидных пленок и уноса газа, они должны были учитывать скорость стробирования, которая во время заполнения должна быть не выше 0,5 м/с. Они обнаружили, что при использовании песчаной формы скорость в затворе быстро увеличивалась, как только жидкий металл попадал в полость детали, что из-за эффекта фонтана вызывало сильную турбулентность. Но с помощью 3D-печатной формы процесс заполнения был однородным, а скорость затвора оставалась постоянной, так как они смогли добавить в конструкцию открытый стояк.
Программное обеспечение использовалось для измерения скорости стробирования в поперечном сечении области слитка во время заполнения обеих форм, и вы можете видеть различные скорости в центре слитка на рисунке ниже.
Процесс состоял из четырех этапов:
- Высокая скорость ввода, создаваемая для обоих методов, достигает 1,10 м/с при литье в песок и 0,55 м/с при литье 3DP
- Скорость уменьшалась и оставалась постоянной в течение большей части процесса заполнения на уровне около 0,90 м/с при литье в песок и около 0,48 м/с при литье в 3DP
- Скорость продолжала снижаться до 0,63 м/с при отливке в песок, но оставалась постоянной при отливке 3DP
- Скорость оставалась постоянной для обоих методов по сравнению с предыдущими значениями, но значительно уменьшилась по мере завершения процесса заполнения
Из-за высоких скоростей в формах во время заполнения может возникнуть эрозия, в результате чего пострадавшие участки будут оторваны. Существует более высокая вероятность эрозии при отливке из песка из-за эффекта фонтана, но это уменьшается при использовании формы 3DP, поскольку профиль скорости легче контролировать.
Затем деталь затвердевает после заполнения пресс-форм. Во время заполнения температура формы повышалась, а затем понижалась во время затвердевания.
- “Температура литья в песок оставалась одинаковой в полости детали при температуре около 710 ° C",-заявили в команде. “Однако температура формы 3DP составляла около 675°C. Более низкая скорость охлаждения была получена в песчаной форме из-за низкой теплопроводности песка и большей толщины формы. В отличие от этого, меньшая толщина и более высокая теплопроводность формы 3DP облегчали поток тепла”.
Для заполнения формы для литья песка потребовалось 5,24 секунды, а для затвердевания детали - 541 секунда, по сравнению с 2,20 секундами заполнения и 378 секундами затвердевания в 3D-печатной версии.
- “Меньшее время затвердевания означает более быстрый коэффициент охлаждения, что приводит к повышению производительности и улучшению механических свойств отливок”, - пояснили они.
Кроме того, изготовление 3D-печатной формы заняло всего десять часов, в то время как литье из песка заняло почти 24 часа, так как они должны были сделать рисунок из двух частей и сгладить его поверхность.
Шероховатость часть выполнена с литье в песчаные формы пресс-формы имеет среднее значение Ра = 3.70 мкм в слое строительство и направлении Ра = 4.53 мкм в противоположную сторону, но при этом шероховатость оказалась даже ниже, в слое строительства направлении на 3D печатные части, он был Ра = 7.07 мкм в противоположном направлении, за счет эффекта ступенек мы часто видим в 3D-печати.
- “Что касается точности размеров, в то время как эффект лестницы на поверхности формы 3DP является наиболее важным аспектом для контроля, в форме для литья песка критическим аспектом является точность размеров рисунка”, - пишут исследователи.
При анализе качества размеров детали были отсканированы, и Geomagic Control X снова использовался для обработки облаков точек. Среднее отклонение между деталью и рисунком для литья из песка составило 0,76 мм, но для 3D-печати -0,43 мм, что показывает, что “технология литья 3DP позволяет изготовить более точную деталь, чем литье из песка”.
Наконец, исследователи сделали продольный разрез в деталях, чтобы проанализировать, что вызвало захват газа и пористость бифильмов в отливках.
- “Микроструктуры поперечного сечения формованных деталей показали складчатые формы и подачу воздуха при литье в песок, что может быть вызвано сильной турбулентностью и оксидной пленкой, присутствующей в расплаве во время процесса заполнения”,-пояснили в команде. “С другой стороны, пористость, обнаруженная в деталях, изготовленных с помощью формы 3DP, соответствует усадке; в процессе заполнения оставшееся связующее испаряется, создавая точки зарождения. Таким образом, поры образуются в результате усадки и смеси усадки и захвата газа".
Поверхностные дефекты были обнаружены только на детали, изготовленной с помощью формы для литья песка, и одним из них был сам песок.
“Участки песка были оторваны потоком металла, всплыли на поверхность, а затем были захвачены расплавленным металлом. Основная причина этого дефекта была связана с неравномерным уплотнением формы или высокой скоростью жидкости, способной повредить форму”, - написали они.
Исследователи пришли к выводу, что использование 3D-печати для изготовления литейных форм было возможным и “адекватным” в качестве альтернативы литью в песок, поскольку это значительно сокращает время и позволяет создавать более сложные геометрии.
BinderJet 3D принтеры позволяют изготавливать песочные литьевые формы со сложной геометрией и высокой точностью. Формы изготовленные на BinderJet 3D принтерах AFS нашли свое применение в аэрокосмической отрасли, ВПК и машиностроении.
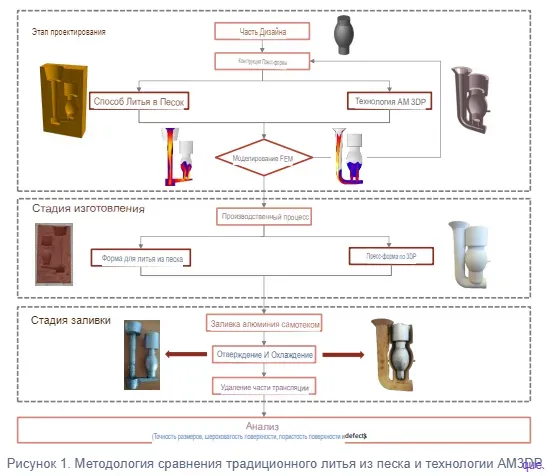
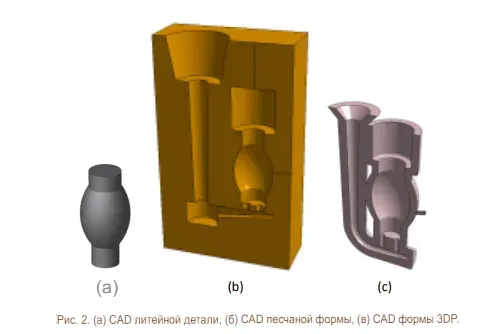
Рис. 2. (а) CAD литейной детали, (б) песчаной формы, (в) CAD литьевой формы для 3Д печати

Рис. 3. Схема процесса гравитационного литья
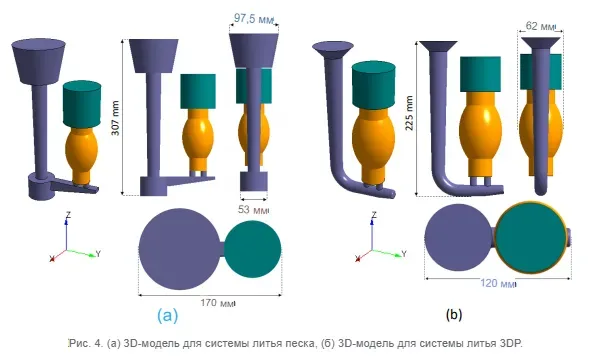
Рис. 4. (а) 3Д модель для системы литья песка, (б) 3Д модель для 3Д печати формы
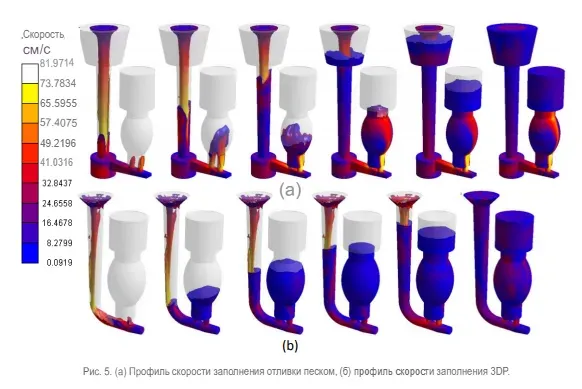
Рис. 5. (а) Профиль скорости заполнения отливки в песок, (в) профиль скорости заполнения 3Д печатной формы
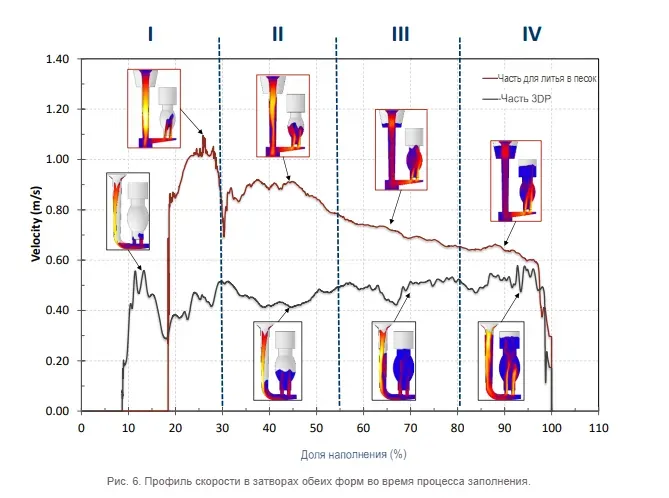
Рис. 6. Профиль скорости в затворах обеих форм во время процесса заполнения
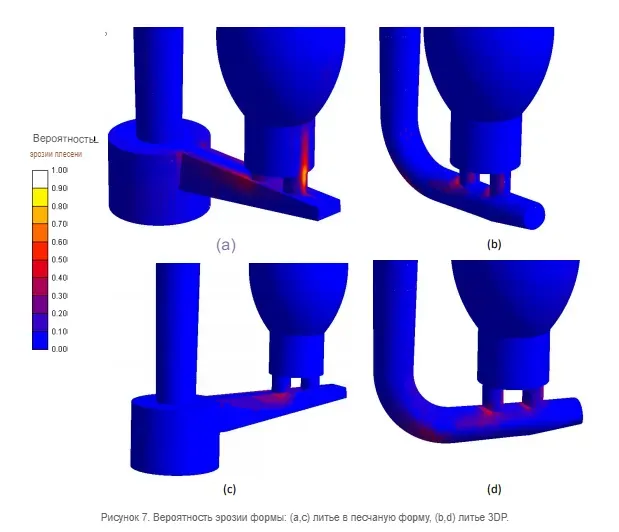
Рис. 7. Вероятность эрозии формы (а, с) литье в традиционную песчаную, (b,d) литье в форму изготовленную на 3Д принтере